Our team is composed of Professionals with experience obtained through work in the most representative Japanese Manufacturing Companies.
List of specialized consultants by purpose
人材育成TPSトレーナーHuman development5SIE工場の立上げ支援Quality improvement Cost reductionProductivity improvementInventory controlLead time reductionSafety improvement Human resources developmentIotTPS trainerManagement improvement Equipment maintenanceProduction technologyDXOthers工場の立上げ支援List of specialized consultants by industry
AutomobileElectric and electronicArchitecture / ConstructionChemistryWhite collarHousing equipmentWarehouse logisticsMedicineMetalFoodDI/IT/ DXOthersTakeshi Kawabata
Former DENSO Corp. Production Engineering Division
Learned and implemented the Toyota Production System directly from Toyota Motor Corporation. Also experienced in two new factory constructions and one existing factory renovation, managing construction schedules and budgets as planned, and realizing information and logistics optimization from the factory entrance to exit.
Responsible for the construction of Japan's largest single factory building at the time, covering 120,000 sqm.
Field of expertise
#Others#工場の立上げ支援
Professional industry
#Automobile#Electric and electronic#Metal#Others
ITO, Akihiro
Process improvement consultant
He worked for JIT Institute, Tokyo for 20 years.( JIT: Just In Time). During this period, he has learned Just In Time philosophy and method of improvement of productivity in manufacturing plant. Continuously he has been engaged in effective introduction process of Production Management System to small and medium enterprise and even big enterprise.
Field of expertise
#Productivity improvement#Lead time reduction#Iot#工場の立上げ支援
Professional industry
#Automobile#Electric and electronic#Others
Nobutoshi Nagaya
Former Toyota Motor East Japan, Inc.: Technical Supervisor & Advisor, in charge of PS (Production System) and TQM (Total Quality Management) projects.
Former Kanto Auto Works: Executive Managing Director, Deputy Head of Production Technology Division, in charge of overseeing overseas business.
Directly learned the essence of TPS (Toyota Production System) from Shin Uchikawa, one of the four lieutenants of Taiichi Ohno, former Vice President. Handled the introduction of the Toyota Production System to various companies both domestically and internationally.
Professional industry
#Automobile
Kouichi Ikemoto
Former Toyota Motor Corporation employee, Head of Press Production Technology Departmen
Practical guidance in the Toyota Production System. Specialist in press mold and press production technology. Provides practical instruction across a wide range of processes including pressing, welding, and assembly at affiliated companies.
Miyuky Honda
Manager of Consulting Division
Mr. Honda has over 20 years of experience with overseas accounts in Japan.
KOJIMA, Kazuhiro
Digital Innovation/Information Technology Design /Digital Transformation Consultant
A consultant at the forefront of practical implementation, specialized in cutting-edge technologies such as AI, RPA, low-code, IoT, and data science.
With a Master's degree from the University of Tokyo, it is leveraged by profound knowledge and experience to lead in the realms of DX and generative AI. The insights and practical approaches have been recognized and highly esteemed in prestigious forums, including invited lectures at the University of Tokyo's Center for Manufacturing Management and the Japan Warehousing Association.
Field of expertise
#DX
Professional industry
#DI/IT/ DX
AOYAMA, Matsuki
Former Motomachi Plant Section Chief, Toyota Motor Corporation (OB)
He has been involved in GPC since its establishment and has trained and mentored a wide range of personnel from new recruits to supervisors in overseas human resource development.
Field of expertise
#Human development#TPS trainer
Zenji Kosaka
Former employee of Toyota Motor Corporation, Deputy Plant Manager at the Head Office Plant
Practiced under the mentorship of Taiichi Ohno during the formative years of the Toyota Production System.
Adhering to the motto, 'Show by doing, explain by talking, let them try, and must praise to motivate people,' I promote improvements where people play the leading role. Expert in machining and assembly
Tsuyoshi Ishigamori
Safety and Health Management Consultant
As a full-time health and safety officer, He worked with a major manufacturing company for disaster prevention and health hazard prevention for 15 years. In safety management, He has enhanced activities to reduce the 1,000-person rate, frequency rate, and strength rate, and are in charge of foreman education and new graduate education instructors as RST. In Safety management, the obligations of business owners after conducting health examinations and stress checks have become established. In addition, based on his experience in personnel and general affairs, we explained the Labor Standards Law, the Industrial Safety and Health Law, and related laws and regulations by rank, and enhanced the system to prevent mental insufficiency due to long working hours. We will continue to make efforts so that business owners will not be questioned by the "safety consideration obligation".
Pushpakumara, Thilak
TPM and Lean Management Consultant
Thilak has trained more than 50,000 executives and managers at different levels of 300 leading organizations in Sri Lanka and overseas.
Institute of Lean Management (Pvt) Ltd- Founder & the CEO of the Institute of Lean Management (Pvt) Ltd,
TPM and Lean Management Consultant and the Managing Director of Lean Solutions (Pvt) Ltd, Bangladesh.
Field of expertise
#Quality improvement #Cost reduction#Productivity improvement#Management improvement
Professional industry
#Automobile#Electric and electronic#Others
List of specialized consultants by purpose
人材育成TPSトレーナーHuman development5SIE工場の立上げ支援Quality improvement Cost reductionProductivity improvementInventory controlLead time reductionSafety improvement Human resources developmentIotTPS trainerManagement improvement Equipment maintenanceProduction technologyDXOthers工場の立上げ支援List of specialized consultants by industry
AutomobileElectric and electronicArchitecture / ConstructionChemistryWhite collarHousing equipmentWarehouse logisticsMedicineMetalFoodDI/IT/ DXOthers
3 reasons why we are chosen
REASON
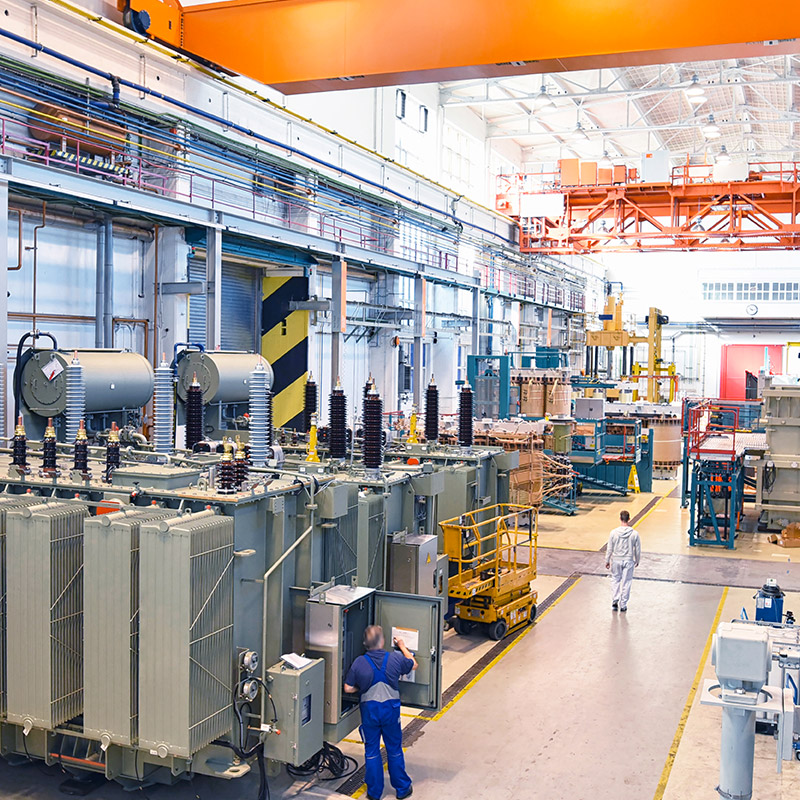
REASON 1
Improvement experience of
more than 1,500 companies in 40 countries
There must be the shop floor issues that cannot be solved by your own company alone. Improvements and reforms for manufacturing industry to survive, regardless of country or industry, need development of your human resources through practical experiences of improvement, and strengthening of your production system base.
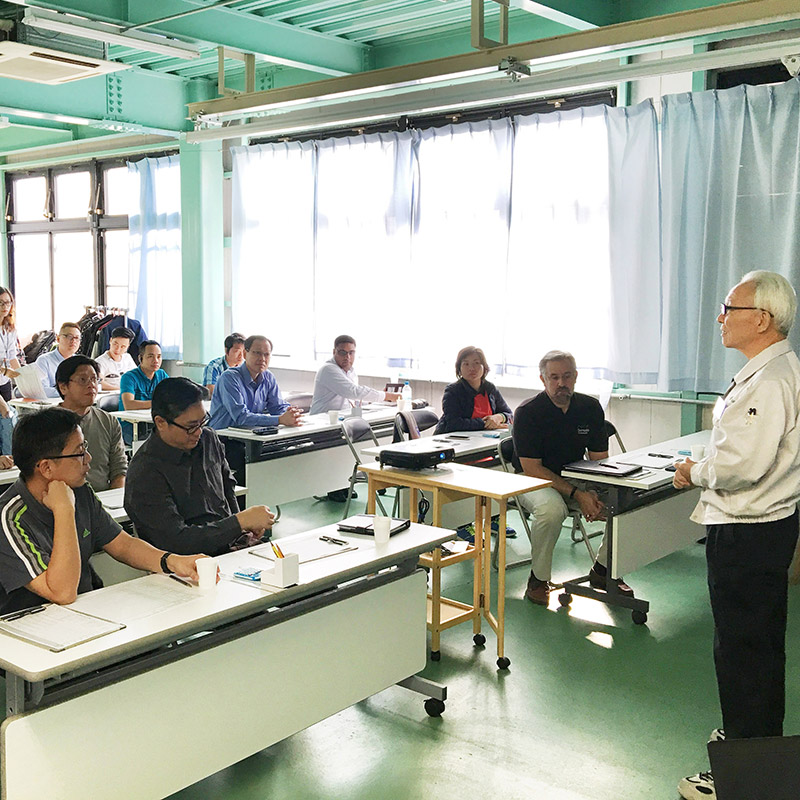
REASON 2
Consulting that shop floor workers
acknowledge our superiority and be pleased
In conventional consulting styles, there was a distance between consultant and the shop floor because it was promoted mainly consultant and management executives. Our consultant can provide a guidance without a distance between consultant and the shop floor through the guidance based on the “seeds of improvement” in a concrete way, instead of “finding fault” like a critic.
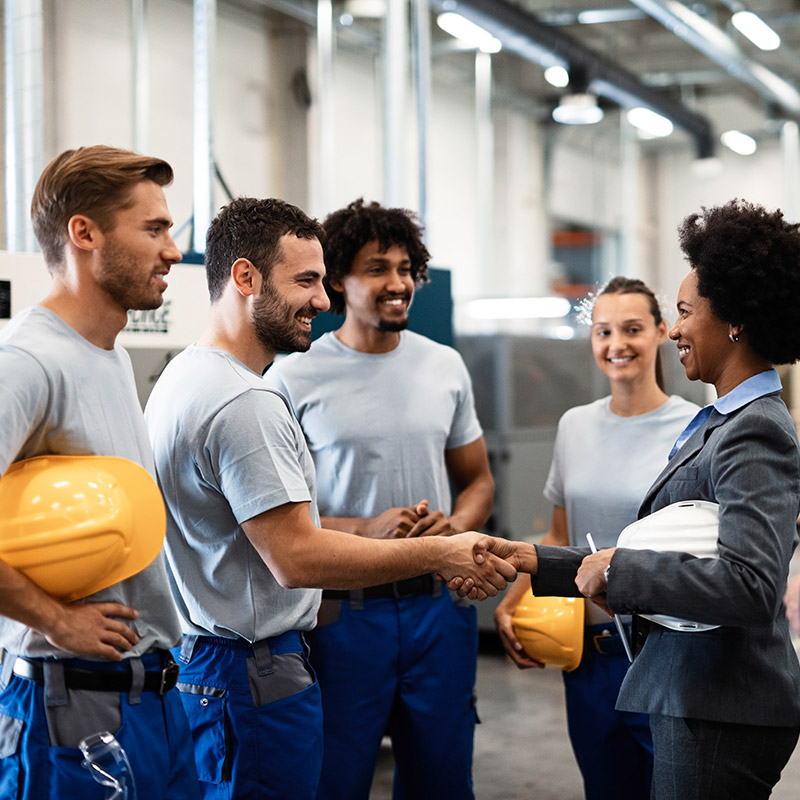
REASON 3
Continuous improvement will continue
even after the end of guidance
While strengthening “human resource development”, we focus on the “overall flow” from design to purchasing, manufacturing, logistics, and production control, and provide guidance that matches the actual situation of your company. Continuous improvement will continue even after the end of guidance through the guidance that is acceptable to the shop floor workers.
Consultants from major companies
with experience in over 40 countries will respond.
Please feel free to contact us.
If you are in a hurry, please call us.
(Japan time)
Open 08:30 – 17:30
Except for Saturday, Sunday, holidays, Year-End and New-Year holidays